Injection moulding performs a fundamental component in the production of the goods we rely on every day. When you comb your hair, button up your shirt, secure your toddler in their vehicle seat, or open a bottle of water, it was all created through injection-molding technology. Injection molding permits producers to mass produce comparable gadgets with greater value efficiency by using injecting polymers (like plastic) into premade molds to shape them into desired shapes.
Molds are designed by way of commercial designers and engineers, built via mold-makers using steel consisting of aluminum or metallic depending on the application, with more than one cavity constituted of identical or specific cavities to each element. Once assembled, precision machined components are then precision machined by using CNCs until completed - this streamlined production technique enables reduced production times as well as errors or disasters for the duration of injection molding processes.
Once manufacturing starts, the polymer is injected below high pressure into each hollow space of a moulded part beneath strain. A mold-maker normally creates a cooling cycle to prevent the crystallization of polymer during injection and ensure exceptional parts. Furthermore, cooling also prevents bubble formation in moulded parts.
Cosmetic rejects in injection molded elements can frequently be the result of trapped fuel bubbles. Not simplest can these disrupt product aesthetics and physical houses, but they may even compromise them entirely. To mitigate such problems and troubleshoot efficiently, it is vitally critical that one understands why bubbles shape and the way satisfactory to address them.
Ratchet mechanisms are embedded within each flange member and cowl member. When rotated at torque same to or extra than a predetermined degree, they race the duvet member towards the flange member to save you its engagement through the ratchet mechanism, proposing resilient claw elements 37a that join them each.
Anti-shaving projections are placed on flange individuals to prevent shaving of parting lines by way of tools. A chamfering profile allows manual those projections even as their recess prevents them from coming in touch with mold side walls for the duration of machining operations.
Fuel tank caps function as a conductive cover member and discharge projection that function together to discharge static energy saved within it to the filler neck. The projection's extent resistivity needs to be less than that of its figure cover member, with an inlet closed with the aid of this projection with the intention to hold constant discharge distance irrespective of when or how the cap is closed.
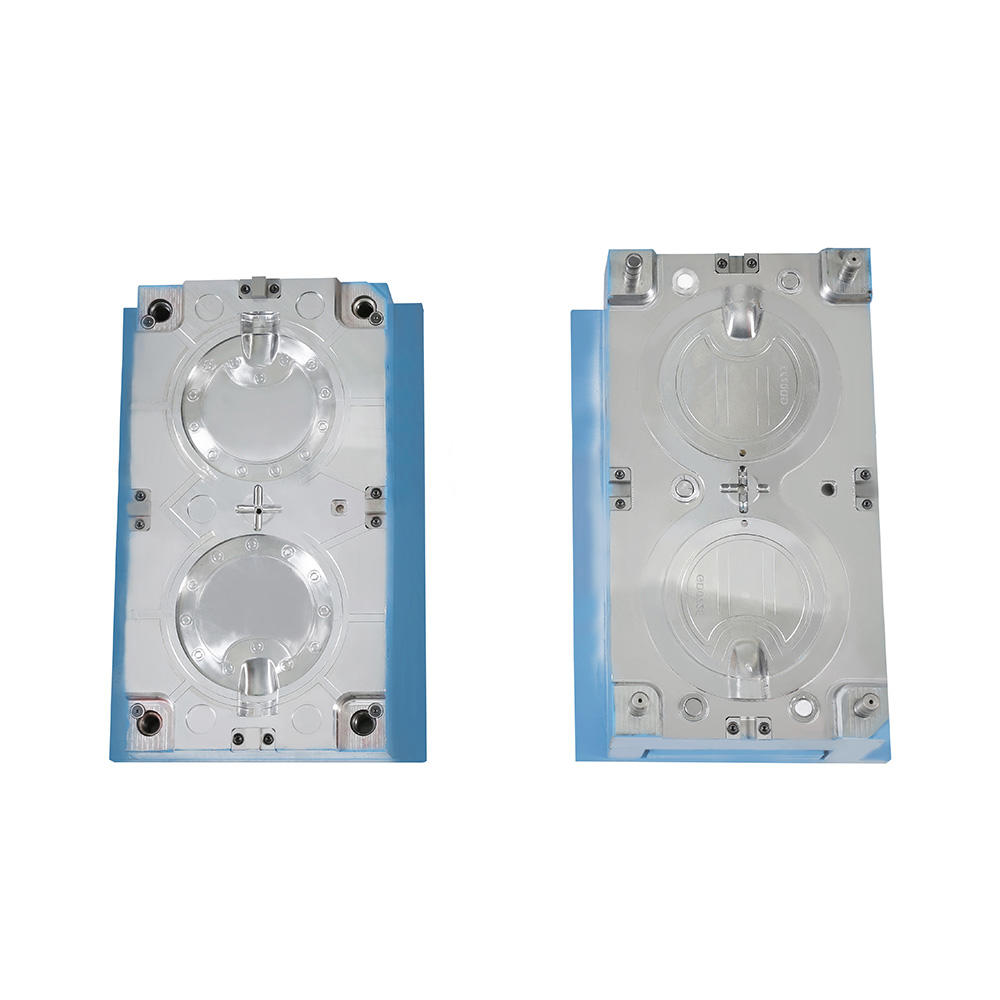