Car bumpers are a critical safety feature on all cars. They assist in protecting automobiles in opposition to harm due to collisions with other motors or stationary objects and help shield pedestrians from accidents because of low-velocity collisions with shifting motors. A car bumper can be composed of diverse substances including metals which include metallic and composite substances like carbon fiber or fiberglass depending on its specific desires and the molding manner used at some stage in production.
To ensure the final vehicle bumper is secure and strong, top-notch care has to be taken in designing its mold. This may include developing a detailed 3D version of its capabilities as well as specifying materials used at some point in production. Injection moulds are the maximum typically used automobile bumper mildew, working via injecting warm plastic or rubber into an empty mildew hollow space earlier than cooling and hardening into its preferred shape to form the completed product. Other car bumper mildew kinds include blow and compression moulds which work by using the use of air or pressure to form plastic into molds.
Bumper injection molds may be complex and require excellent precision to produce well-formed plastic bumpers, especially large, skinny-walled bumpers with extraordinarily inflexible systems that have to face up to rugged use. In order to do this, designers of bumper injection moulds need to don't forget both physical houses of plastic in addition to simulation software whilst optimizing their layout of the mold.
Injection moulds for automotive bumpers may additionally be characteristic of various cooling and ejection systems to meet the precise requirements of vehicle producers. Of key importance is ensuring that the mould can face up to strain and temperatures related to injection moulding processes and its ejection system can accommodate its length and complexity of bumper.
An injection mildew for auto bumpers needs to encompass an ejection system able to supply enough energy and pace for you to eject molded plastic from its mildew, and save your rubber from adhering lower back inner after demoulding. Therefore, its design needs to encompass excessive accuracy and electricity in addition to being clean to keep or restore.
The temperature of the injection mildew also has a first-rate effect on plastic mould first-rate. Temperature is decided by using factors like cloth and performance of the injection system; conformal waterways frequently comply with contours in bumper injection moulds for uniform cooling; it's critical to choose an injection system with suitable length and overall performance to get gold standard effects from these moulds.
Once a bumper injection mildew is complete, it has to be very well examined and maintained to ensure the right operation. This can also contain strolling taking a look at moldings to take a look at its overall performance as well as making any necessary changes or upkeep.
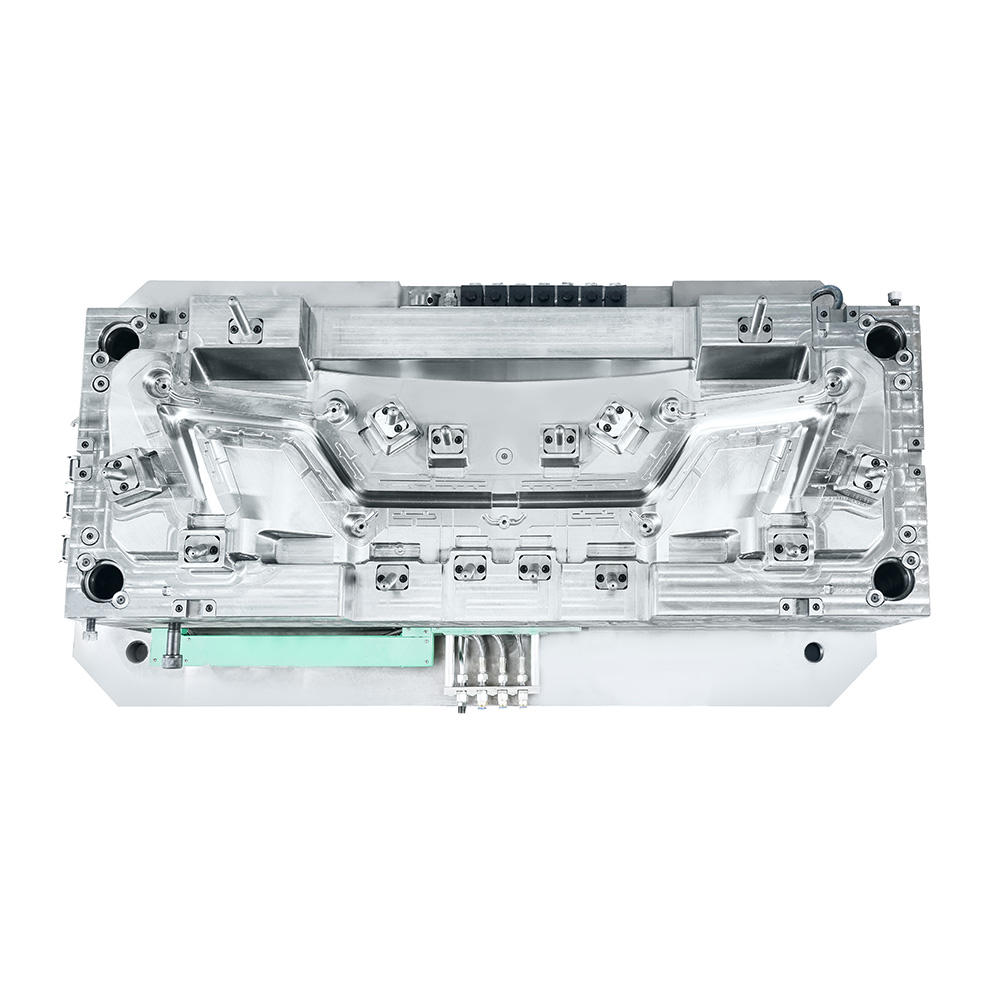
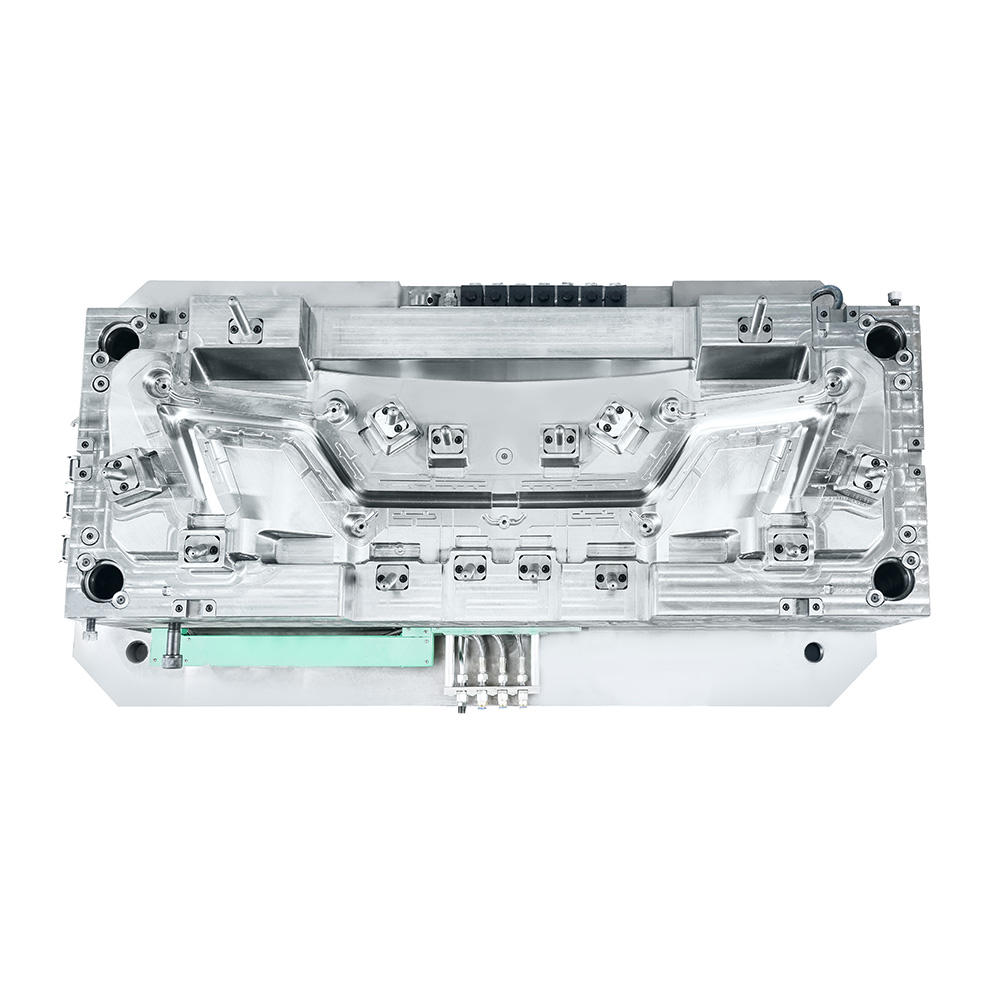