At the forefront of every car lies its grille: an integral component of its engineering and design. Not only does it look good, but its main function is also aerodynamic flow enhancement and drag reduction. Engineers and designers spend countless hours designing the perfect grilles to complement each vehicle - it's fascinating finding pieces of vintage automotive history like this original grille mold for 1985-1989 Dodge Aries at flea markets!
Molds are made out of durable material. A master pattern accurately portrays the size and shape of the grille that will be produced; then this master pattern is used to form the mold which will attach to an injection molding machine for production. Once created, each grille produced is subjected to rigorous quality assurance testing to ensure it satisfies client specifications.
Automobile grilles were traditionally manufactured using traditional metal stamping processes. While this method offered limited design possibilities due to limited steel and other metals being available at that time, its economic design often determined what would ultimately become available as grille options.
Modern plastic injection molding technology has made it possible to produce automobile grilles that are far more complex and innovative than before. Not only are they more attractive and durable; but their production is faster, cheaper, and more environmentally friendly as well allowing for a higher level of customization that better matches individual customer requirements.
Manufacturing a car grille mould requires extensive expertise and precise execution. There are a variety of factors that could impede its quality, such as surface defects, weld marks, silver wire, color separation, or material degradation; to mitigate such risks it's crucial to utilize proper injection molding techniques while cleaning and maintaining your mold regularly.
An important step in producing high-quality car grille moulds is selecting the appropriate materials. Polypropylene (PP) is one of the most frequently used materials due to its superior strength, toughness, and lightweight properties - as well as being very versatile as it can easily be formed into any desired form.
For optimal automobile grille results, it is crucial to choose a manufacturer with extensive experience in this area. A well-versed mold manufacturer will be able to deliver top-quality products at an economical price point while offering additional services like prototyping and inspection - all designed to deliver outstanding results for their clients.
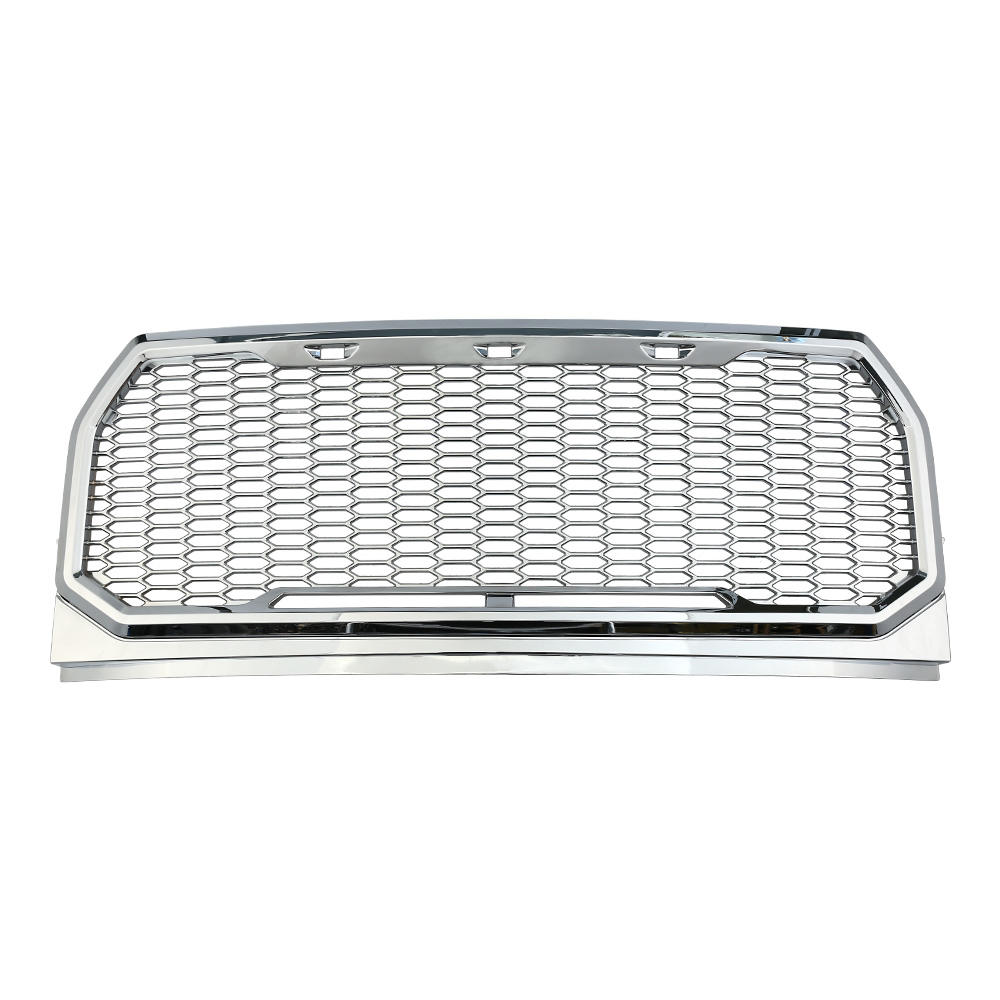
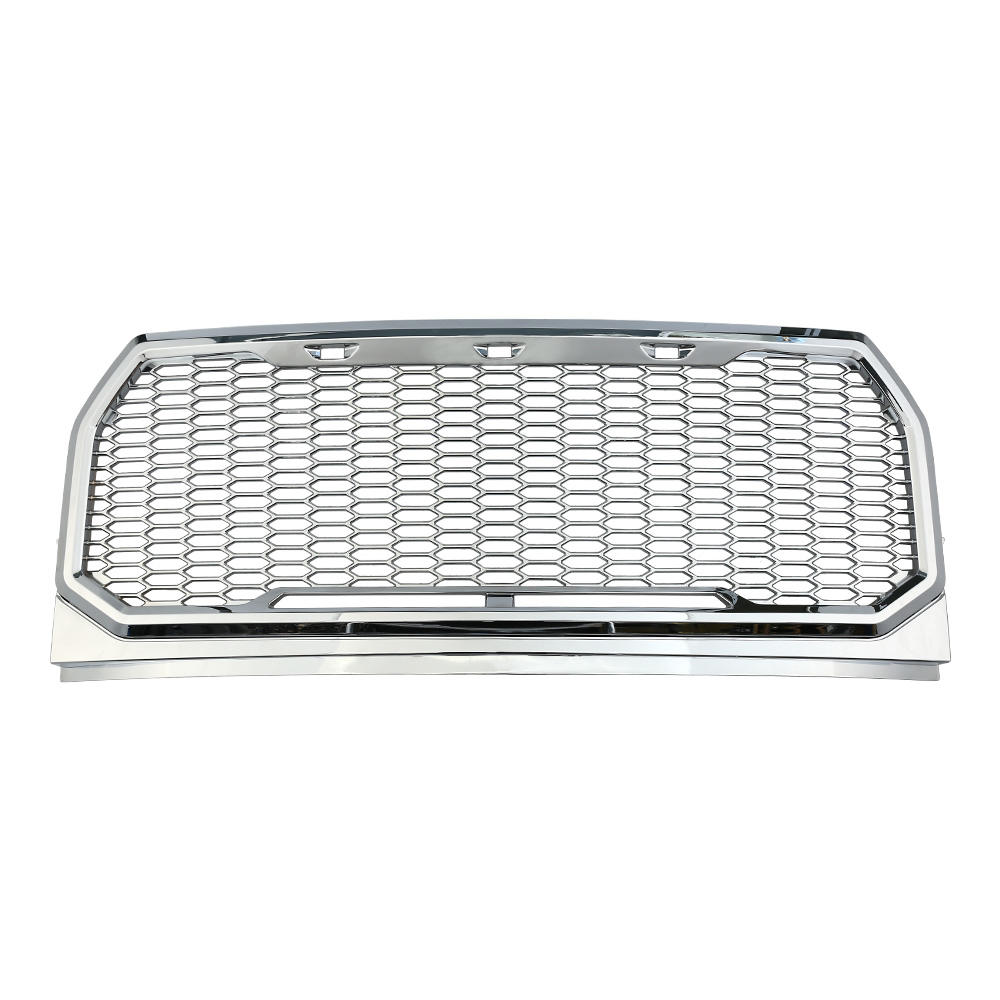